Промышленные предприятия Среднего Урала ежегодно вкладывают сотни миллионов рублей в повышение энергоэффективности. Крупные игроки рынка не жалеют средств на внедрение новых технологий и закупку современного оборудования. Они понимают, что, во-первых, благодаря этому повышают экономическую эффективность производства, а во-вторых, как правило, при применении таких ноу-хау в разы уменьшается количество выбросов в атмосферу, что благоприятно влияет на экологию. В конечном итоге все эти меры положительно сказываются на экономике региона в целом.
О том, какие энергоэффективные мероприятия по итогам 2021 года провели крупные предприятия региона, — в материале ЕАН.
Экономия в действии
Динамика потребления топливно-энергетических ресурсов (ТЭР) в Свердловской области с 2007 года постепенно снижается. Итоги 2021 года пока не подведены, но об этом свидетельствуют результаты прошлых лет, и ожидается, что тенденция продолжится.
Данное снижение непосредственно отражается на валовом региональном продукте (ВРП), который является одним из индикаторов состояния свердловской экономики. Как пояснили нашему агентству в региональном Министерстве энергетики и ЖКХ, «энергоемкость BPП измеряется как отношение суммарного энергопотребления региона к величине BPП и позволяет оценить уровень развития экономики региона». Основной объем валового регионального продукта Свердловской области традиционно формируется в промышленном секторе экономики — 44,4%.
По итогам 2019 года BPП региона вырос на 4,4%, суммарное потребление топливно-энергетических ресурсов (ТЭР) по видам экономической деятельности сократилось на 0,4%. Это свидетельствует об эффективности производств, то есть продукция производится с меньшим потреблением ТЭР.
В 2020 году BPП Свердловской области снизился на 7,9%, но тут, скорее, «энергосберегающие» показатели совсем ни при чем. Дело было в наступившей пандемии коронавируса, вводимых локдаунах на предприятиях, приостановке торговли в определенных сферах. Что касается суммарного потребления топливно-энергетических ресурсов, то в 2020 году оно сократилось на 0,2%.
В министерстве не проводят анализ конкретных энергоэффективных технологий, внедряемых предприятиями, поэтому мы попросили рассказать о них крупных игроков промышленного рынка.
"ФОРЭС" и сухая технология
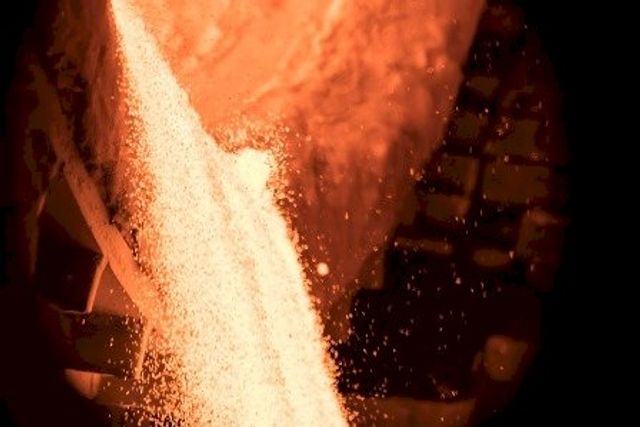
Компания "ФОРЭС" – крупный российский производитель пропантов – в декабре минувшего года полностью перешла на сухой способ изготовления продукции. Переход на иную технологию прорабатывался с 2019 года, в 2020 году компания начала «пилот» и тестовое производство малых партий. А последний этап работ перехода на сухое производство завершен осенью 2021 года на Сухоложском обособленном подразделении компании.
Основные задачи, которые стояли перед предприятием, – это технологическое переоснащение производства и создание резерва для прироста мощностей в будущем. Объем финансирования проекта только за год (с ноября 2020 года по ноябрь 2021 года) составил 800 млн рублей.
Прежняя технология подразумевала использование перемолотого сырья с водой. Оно поступало в башенные распылительные сушила (БРС) и разбрызгивалось с помощью форсунок. В противотоке продуктов горения природного газа образовывалось зерно пропанта. С использованием БРС предприятия «ФОРЭС» работали около 15 лет - тогда данная технология считалась наиболее оптимальной. Технологический переход исключает из производственной цепочки узлы и агрегаты – шаровые мельницы мокрого помола и БРС, которые уже демонтируются.
Как сообщил исполнительный директор «ФОРЭС» Михаил Ловков, прежняя технология производства пропантов характеризуется высокой капиталоемкостью из-за стоимости энергоресурсов и сопутствующих природоохранных мероприятий.
«Реновация позволит сдержать дополнительные расходы на стоимость ресурсов и снизить техногенный, антропогенный факторы для окружающей среды», – объяснил он.
Заместитель исполнительного директора «ФОРЭС» по технологии Василий Плотников акцентирует внимание на том, что самый дорогой во всех смыслах ресурс – это вода.
«Сокращения ее оборота означает, что мы откорректируем выбросы в атмосферу. Из всего объема воды мы выпаривали половину, остаточная влага в виде пара выходила из труб над производством. Другой способ производства позволит сократить выбросы, и сейчас изменения уже видны: над заводскими площадками больше нет клубов пара, как раньше. Особенно заметно это зимой при низкой температуре», - объяснил Василий Плотников.
Помимо «энергетического» и экологического есть и другие положительные эффекты от обновления производственных линий. «Раньше мы старались использовать каждый метр площадей на производстве, а сейчас высвобождаются площади, которые мы можем более эффективно использовать. Задача этого года - пересмотреть планировку, учесть все мелочи и улучшить внутреннюю логистику, чтобы на каждом этапе передела были правильно и удобно организованы условия труда, места доставки и хранения продукции», - рассказывает директор Сухоложского обособленного подразделения «ФОРЭС» Александр Константинов.
В компании подчеркивают, что все работы по модернизации оборудования и переходу на другой способ производства проведены так, чтобы не допустить изменений по качеству и объему производства конечной продукции.
УГМК и уникальная паротурбинная установка
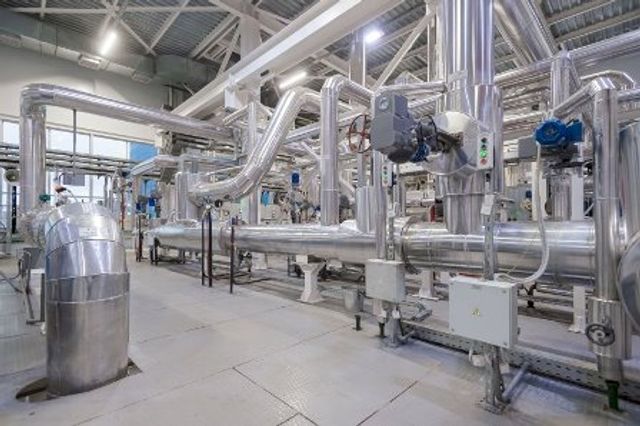
Предприятия Уральской горно-металлургической компании также продолжают внедрять новое энергоэффективное оборудование. В минувшем декабре на Среднеуральском медеплавильном заводе в Ревде торжественно открыли паротурбинную установку для использования парового потенциала котлов-утилизаторов обеих печей Ванюкова. Инвестиции в проект составили порядка 590 млн рублей.
Заключение энергосервисного договора с ООО «Штарк Энерджи Ревда» о строительстве на территории завода паротурбинной установки было получено в феврале 2019 года. Проект реализован по схеме BOT-контракта: строительство паровой турбины на средства инвестора с последующей передачей объекта в аренду предприятию на 12 лет. Затем турбина передается в собственность завода для дальнейшей эксплуатации.
Установка будет вырабатывать электроэнергию и тепло за счет пара, получаемого при производстве черновой меди в котлах-утилизаторах печей Ванюкова. Сейчас избыточный пар уходит в атмосферу. Паровая турбина будет дополнительно вырабатывать для предприятия 53,5 млн кВт/ч электрической и 35 тыс. Гкал тепловой энергии в год. Реализация данного проекта позволит повысить энергоэффективность производства и снизить объем приобретаемой предприятием электроэнергии.
«Данный объект не только вырабатывает электроэнергию, но и использует тот пар, который уходил буквально в трубу. Мы получаем замкнутый цикл. Этот проект – настоящий прорыв, и он будет востребован и на других предприятиях УГМК», - подчеркнул на открытии генеральный директор УГМК Андрей Козицын.
Паротурбинная установка – это второй проект, который реализован компанией «Штарк» на СУМЗе. Первым объектом стала газопоршневая мини-ТЭЦ мощностью 21,5 МВт, тепловой мощностью 17,9 Гкал/час, введенная в эксплуатацию в декабре 2014 года. Оба источника собственной генерации в сумме будут вырабатывать 40% электрической энергии от общего потребления завода.
«С запуском паровой турбины мы продвинемся по всем направлениям – в плане как энергоэффективности, так и энергобезопасности. Это комплексный подход в решении производственных задач, который будет применяться и в дальнейшем при реализации следующих проектов», – отметил директор СУМЗа Багир Абдулазизов.
Уралмашзавод и новые котельные
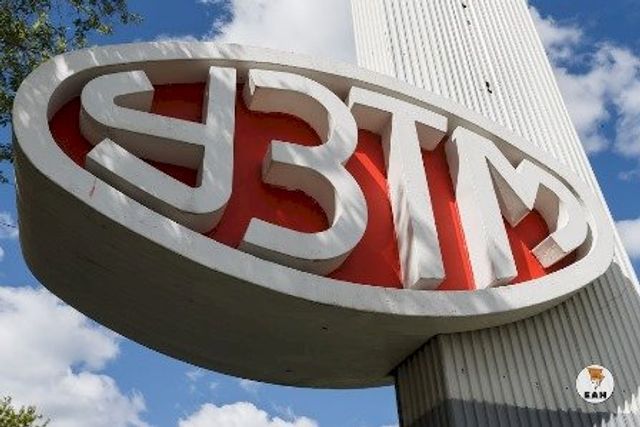
Уралмашзавод (входит в Группу УЗТМ-КАРТЭКС) в 2021 году построил на предприятии две новые газовые котельные мощностью 15 МВт и 7,5 МВт.
Строительство новых котельных – самые масштабные проекты УЗТМ и ИЗ-КАРТЭКС в сфере энергоснабжения за последние 20 лет.
Как отмечают в пресс-службе УЗТМ, это инновационные проекты. Котельные полностью автоматизированы и оснащены по последнему слову техники. Оборудование позволяет гибко регулировать температуру теплоносителя в зависимости от погодных условий. Для подачи в цеха очищенной и смягченной воды используется передовой метод водоподготовки. А встроенные в горелки "умные" датчики и приборы экономят газ и делают работу котельных максимально экологичной. Вывод котельных УЗТМ на номинальную мощность состоялся в сентябре.
«Благодаря новым котельным зимой в производственных помещениях и АБК блоков 10 и 12 будет поддерживаться комфортная для работы температура. Сегодня котельные работают в штатном режиме», – говорит главный энергетик УЗТМ Антон Леушин.
На петербургском предприятии ИЗ-КАРТЭКС энергоэффективность современной автономной котельной уже подтверждена. Газовая котельная была построена там в 2020 году в рамках реализации масштабной инвестпрограммы. В работе котельной используются три котла производства российской компании «ЭНТРОРОС» серии «Термотехник» (два мощностью 6 МВт и один – 2 МВт). Работа оборудования автоматизирована – параметры отопления регулируются в зависимости от внешней температуры воздуха, а запуск тепла не зависит от официального начала и окончания отопительного сезона в Санкт-Петербурге.
«Весь цикл отопления и горячего водоснабжения ИЗ-КАРТЭКС теперь осуществляет автономно. В прошлом отопительном сезоне температура в цехах и АБК поддерживалась в среднем на уровне +20 градусов. Экономия от работы котельной за первые шесть месяцев 2021 году составила более 40 млн рублей», – отмечает главный энергетик ИЗ-КАРТЭКС Алексей Смирнов.
По итогам текущего отопительного сезона на предприятии ожидают получить существенный экономический эффект от использования котельной.
В 2022 году предприятия намерены продолжать работу в энергоэффективном направлении.
Есть новость — поделитесь! Мессенджеры ЕАН для ценной информации
+7 922 143 47 42